
Non-destructive inspection of welds is done using Ultrasonic Flaw Detectors. This is the application and is a key inspection method in this industry to guarantee safety and performance. Welds may be found in all vital infrastructures as well as many important manufactured materials that we use in everyday life. The following are some examples of some of the most powerful and essential applications of ultrasonic flaw detectors: 1. Wood and paper goods are the only typical technical materials that cannot be tested with ordinary ultrasonic equipment.
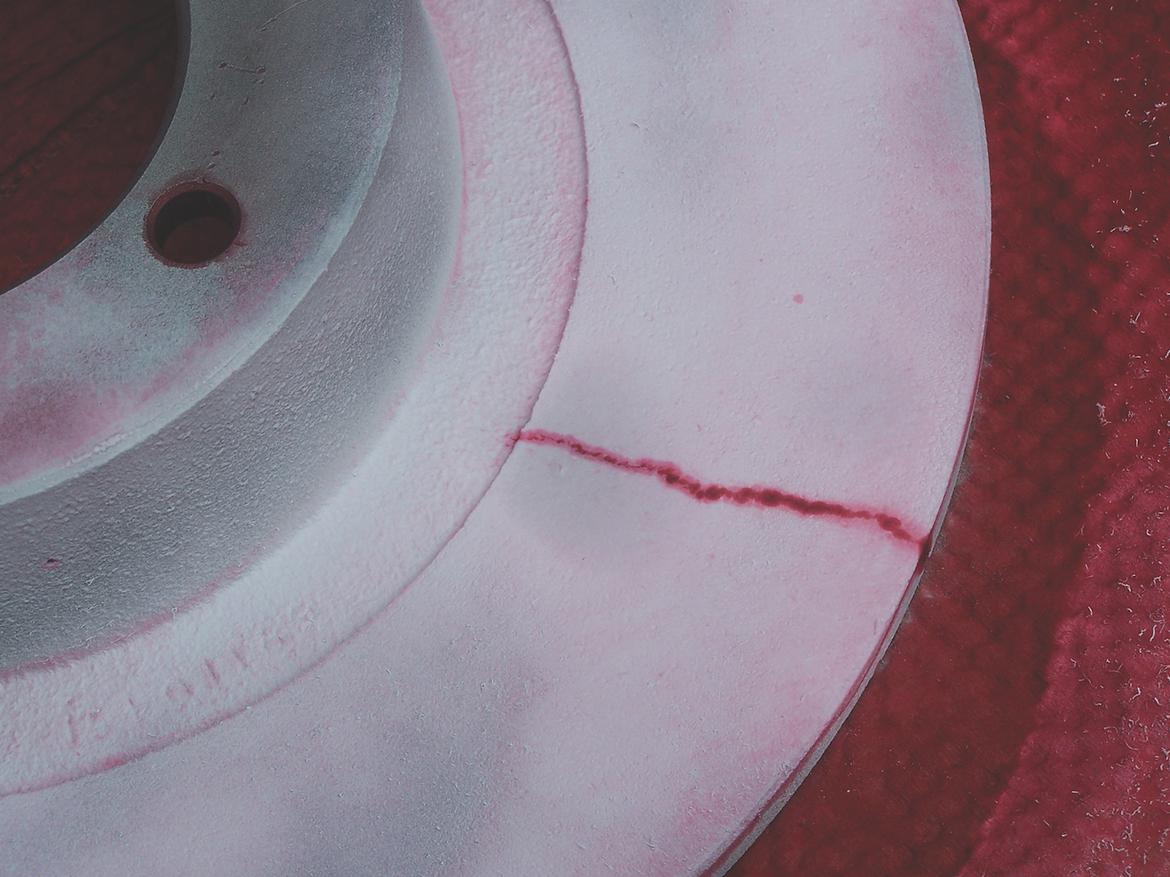
Ultrasonic testing is frequently utilized in industrial applications on metals, polymers, composites, and ceramics. Most Common Applications Of Ultrasonic Flaw Detectors Aerospace, oil and gas, and power generating are all common applications of flaw detectors. A transducer is used in ultrasonic testing to both make vibrations and receive the echoes that are returned, and the returned signal may be transformed into a waveform pattern that can be studied. There are many applications of ultrasonic flaw detectors that include detection of abnormalities in metals, composites, polymers, ceramics, etc. Although flaw detectors are most commonly employed on steel and other structural metals, they may also be utilized on polymers, composites, fiberglass, and ceramics. Ultrasonic Flaw Detection can be used to locate concealed fractures, voids, porosity, inclusions, and other discontinuities in typical solid engineering metals and other materials.
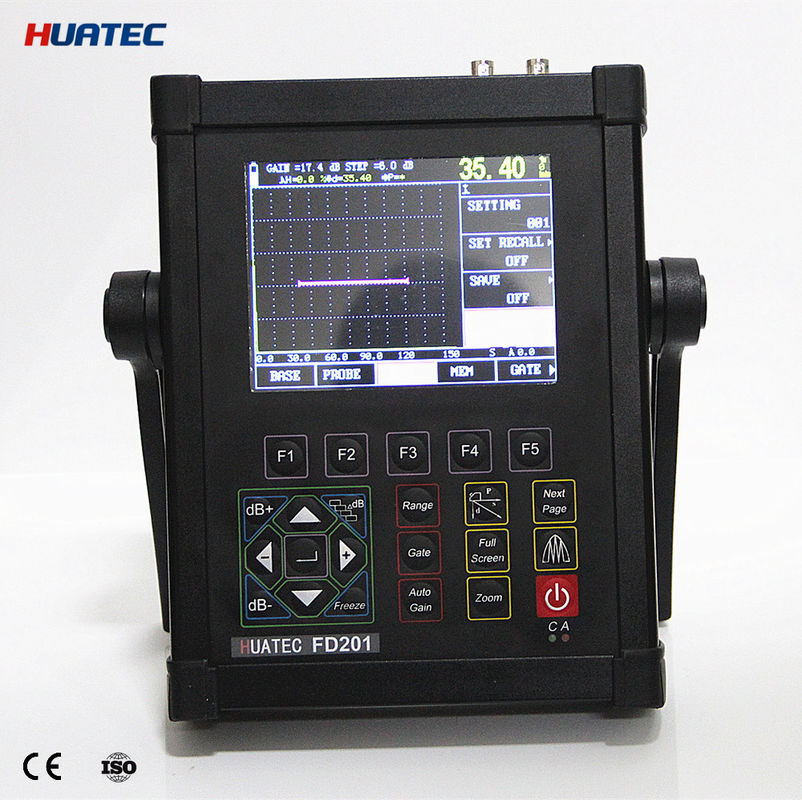
